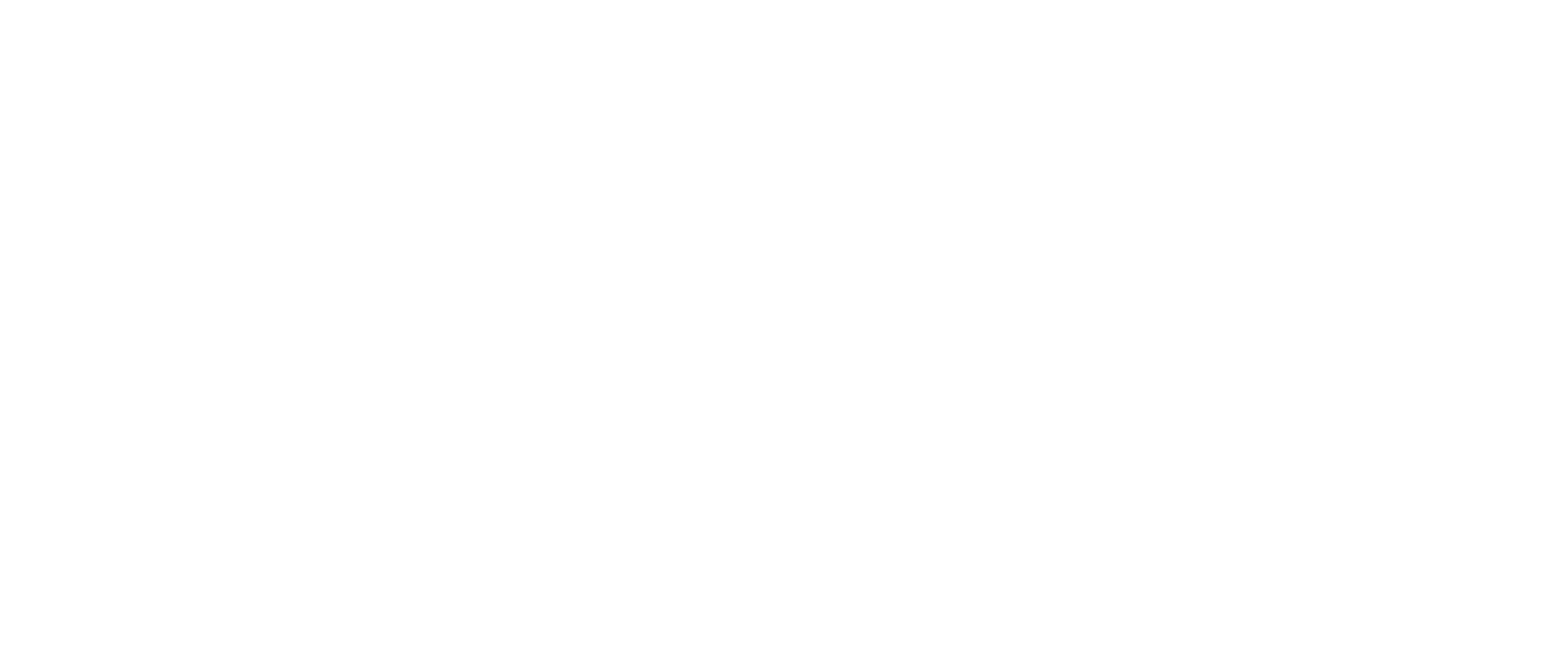
与您一起塑造未来
Burger橱柜是最大的橱柜生产商之一。在舒乐咨询公司的帮助下,他们仅用了6个月的时间便将生产效率提高了16%以上。
《HK杂志》2019年第6期的一篇文章,点击这里阅读全文 点击这里阅读全文
超过100年历史的高品质橱柜
Burger Küchenmöbel GmbH拥有100多年的历史。创始人Otto Aßmann于20世纪10年代开始手工制作厨房家具。上世纪50年代,这家总部位于东德的公司开始从事出口业务,出口国家主要包括当时的西德、荷兰和苏联。在经济形势大好的几年里,随着成品橱柜的需求不断增长,Burger公司也转变其生产方向来适应市场需求,这种成品橱柜也代表了当今的潮流。在90年代初,Burger公司与Bauformat合并,实现稳步发展。
Burger目前有2条生产线,分别生产"Trend"和"Linea"两个品牌的产品。Burger将产品定位在高品质的细分市场,提供有竞争力的产品,特别是在柜体尺寸、柜体门板和拉手类型选择范围上,要多于市场常规型号。
客户可以选择14种柜体花色和180多种门板类型。门板表面材质也包含三胺,木皮,和彩色油漆。除了橱柜,Burger还销售自有品牌的集成电器。产品组合的销售主要由B2C业务中的小型橱柜工作室负责。有时,也通过工程单业务销售产品。2018年,Burger和Bauformat一起创造了2.4亿欧元的销售额。生产量约为14万个橱柜,约由1,000名员工加工完成。这相当于平均每天生产650套橱柜,大约7,000个单元柜。其中,5,000个单元柜在汉堡的Burger工厂完成生产(三班制),2,000个在勒讷的Bauformat工厂完成生产(单班制)。
智能、独立的制造单元
Burger是一家运作良好的企业,且物流系统完善。企业内部有MES系统的大力支持。生产设备使用的也是最先进的,常规情况下,在生产过程中不会出现大的“失误”。近年来,Burger Küchen也一直在不断地进行自动化的升级和优化。几年前,Burger每天只生产1,000个与订单相关的部件。现在,在灵活和高度自动化的生产单元中,Burger可生产8,000个定制的门板和柜体部件。门板的分拣流程也成功地实现了自动化。Burger总是信赖独立的智能生产单元。在机器人单元,所有不同来源(外协的门板、仓库存储的面板、按订单生产的门板等)的门板都会从无序堆垛中被分拣到门板小车中。这种自动化处理的最大优势是保证了流程的完整性并避免了分拣时出现错误,并为Burger节省了人工。然后,通过机械手将小车中的门板上料送到加工中心,在那里进行五金孔位钻孔并自动安装配件。在不久的将来,各单元之间的运输将通过无人驾驶运输系统进行优化。
尽管有着坚实的生产基础,但在过去还是不能实现目标产能。这就是为什么启动 “5000” 项目(每天生产5,000个成品柜)的原因。在这个项目中,为了分析未能达到产能目标的原因,舒乐咨询公司再次对Burger Küchen提供支持。Burger面临着与大多数其他公司一样的问题,多年来,一种“企业失明”的现象悄然而至,这往往导致无法站在“自上而下”的角度来客观地识别问题、分析问题、解读问题,从而能最终找到优化措施。“5000”项目就是为了纠正这种情况。在舒乐公司的支持下,旨在找出产能目标未实现的原因,并制定相应的优化策略。
小变化带来大影响
正如预想的那样,对于一个运作良好的企业,Burger不存在严重的问题。然而,这些年来许多小问题已经渗入到公司的日常事务中,并在“一直都是这样”的借口下存在,随着时间的推移这些问题并没有得到解决。他们主要的问题体现在维护、工作组织架构,生产流程同步以及质量和缺陷管理等方面。就维护而言,问题主要出在“关键设备”上,它们的使用年限在5至12年之间。问题不在于使用长短,而在于缺乏预防性维护。这样的问题一再导致无法预见的故障,最终使生产计划中断。为了防止这种情况的出现,制定了相关的措施来尽可能减少这些问题的发生。这些措施包括识别维修故障以及利用停机期间(例如法定假日或周末)提前进行预防性维修检测。针对不同问题所执行的措施已经大大提高了产能,但这种维护优化的方式必须始终如一地持续下去。
在质量和缺陷部件重新加工方面也发现了可进一步优化的潜力。精益理念,旨在生产过程中不断检测质量,以尽可能地减少不合格部件的附加值,从而避免浪费。在Burger,这一精益理念一直贯穿于整个物流链,以确保所有部件在正确的时间以优良的品质到达组装线,无缺陷。对缺陷的类别进行A/B分类也有助于直接在现场消除小问题。如果柜体的门板存在缺陷,对工厂性能的影响将是原来的2-4倍。这些措施虽然已经开始实施,但还需要进一步完善。
优化和加速了后期生产加工流程。如果部件被标识为缺陷部件,尤其是按订单生产的部件,则会立即创建该部件的重新加工订单。这意味着在上游工序中已经检测到错误,并且可以在组装日期前及时完成补单。这样可以实现完整的组装,不存在部件缺失的问题。为了成功地实施这一流程,必须确定重新加工的顺序。Burger已经定义并持续实施了这一过程。在这方面,重要的是在各部门之间以一种严谨的方式维护已定义的流程和时间规划。只有具备必要的纪律性和连续性,才能做到这一点。
通过协调组装线的周期时间以及加工流程的同步,可以显著提高生产率。在最终生产订单之前进行详细的产能规划,可以及时对某些生产流程中的瓶颈做出反应,从而不会对组装线的周期时间产生负面影响。在自动组装线上,大量配件从“网格”中掉落并被处理,而不是一直收集并返回循环使用。这些配件包括踢脚板配件、抽屉夹和铰链。由此造成的经济损失在六位数范围内。应尽可能消除这种情况,找出问题的原因。不合格的门板体现了物料的另一个“黑洞”。不合格的门板的数量每天约为350至400件。然而,通常可以将这些有瑕疵的部件重新加工,然后再次进入到生产过程中。其目标是节省40%的门板,从而实现每年约100万欧元的节约潜力。
在Burger,普遍存在的技术工人短缺问题在组装区尤为明显。目前正在试图用临时工来代替缺乏熟练工人的问题,但不可能用不合格的工人来建立一支成熟的团队。Burger公司已成立了一个项目用来建设一支长期的、协作良好的高质量组装团队。在这个过程中,管理者必须始终如一地参与团队建设。需要在加强对生产区域的监管,以便监测工作时间和生产流通情况。为了加强这方面的管理能力,必须减少或放弃不必要的行政活动。
得益于所有生产流程的持续改善,即使不采用三班制,Burger计划达到的生产率提升也得以实现。舒乐咨询公司和德国Burger Küchen 之间的成功长期合作成果显著。很高兴看到Burger Küchen在较短的时间内发展成为一家技术领先的公司。
作者:Volker Jahnel, 舒乐咨询公司欧洲区高级经理,负责生产规划和“批量为一”的生产。
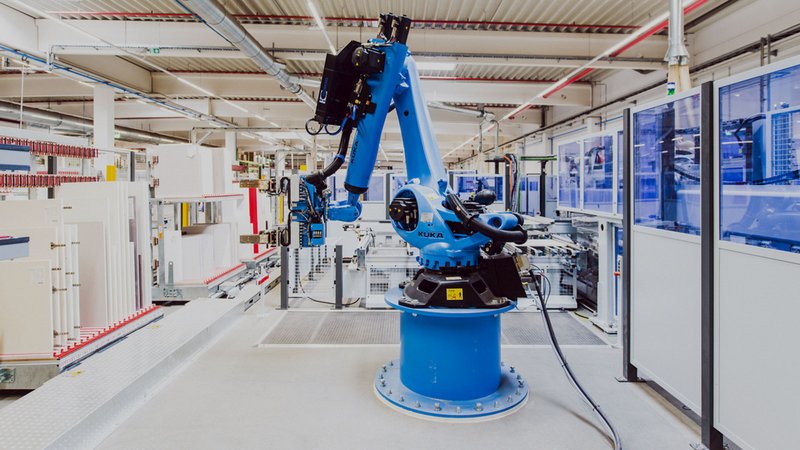
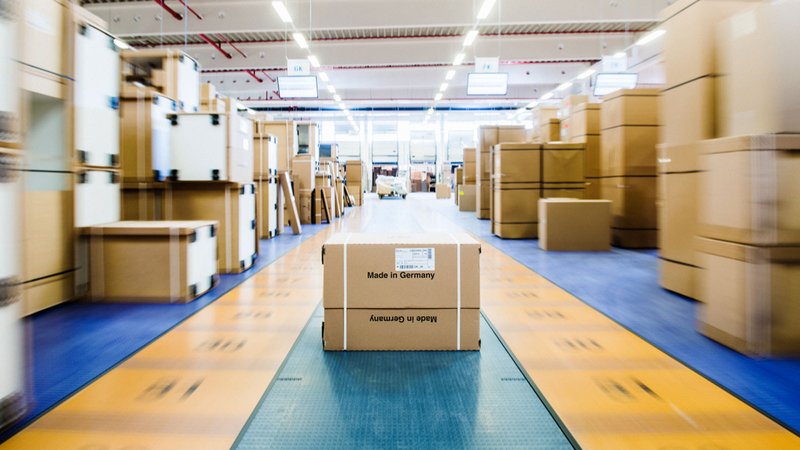
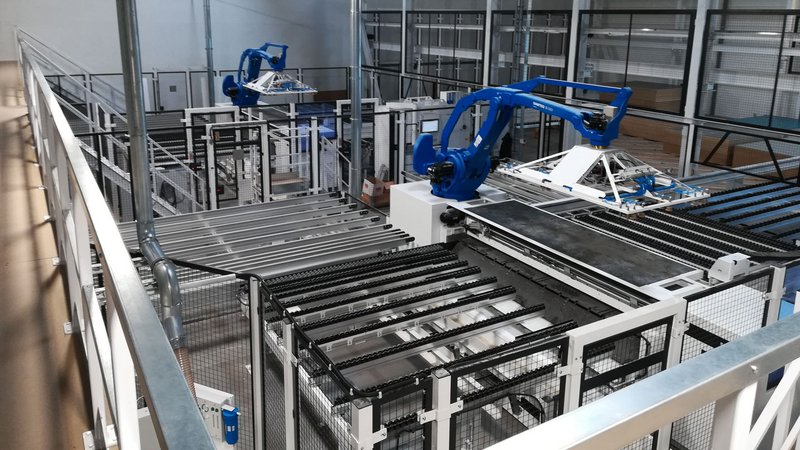
通过与舒乐咨询公司的合作,Burger公司已成为生产技术领先的公司之一。
在舒乐咨询公司的帮助下,Burger公司大大提高了他们的生产效率。
Burger公司应用其高度灵活的生产单元可生产8000个门板和柜体部件。
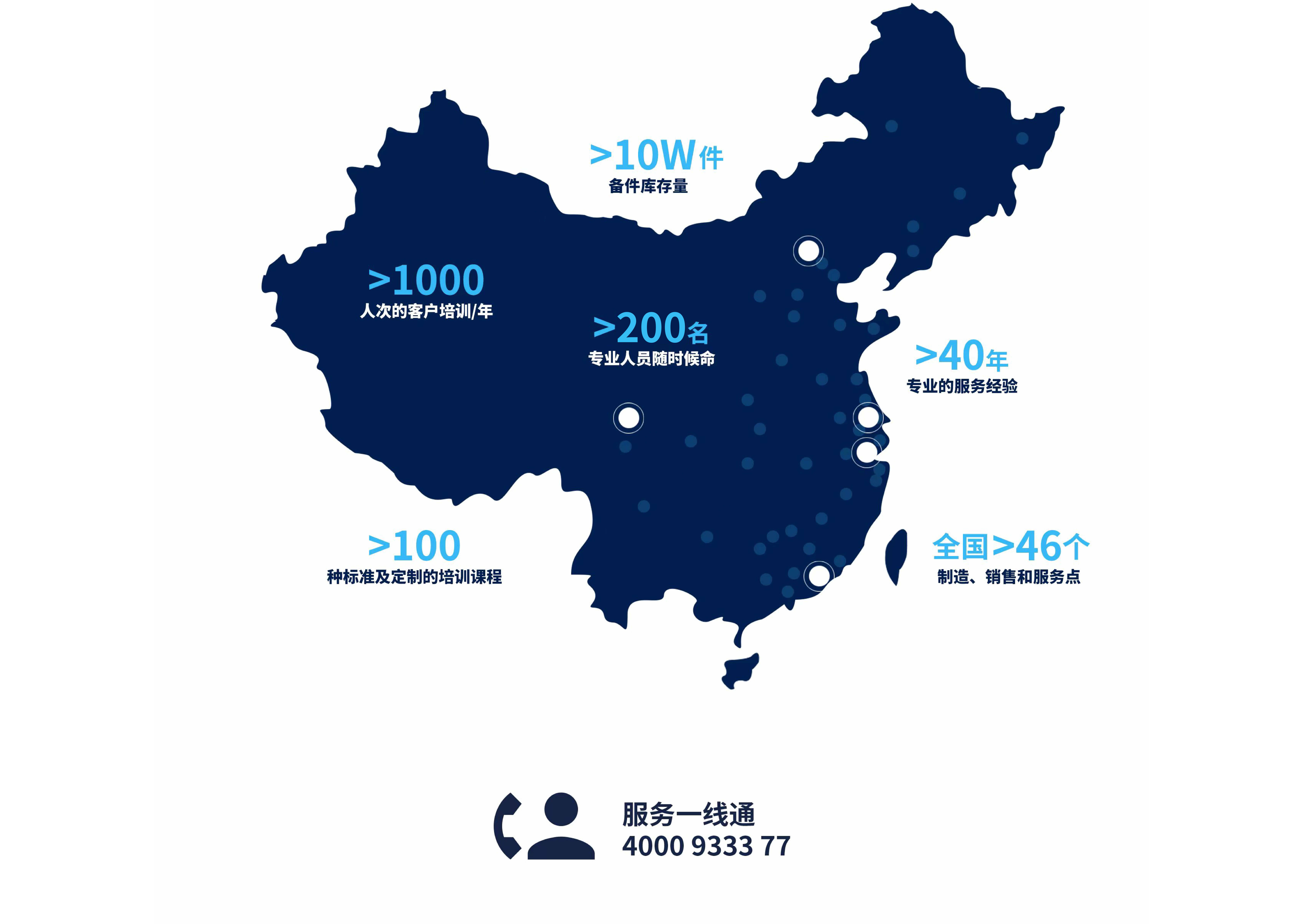