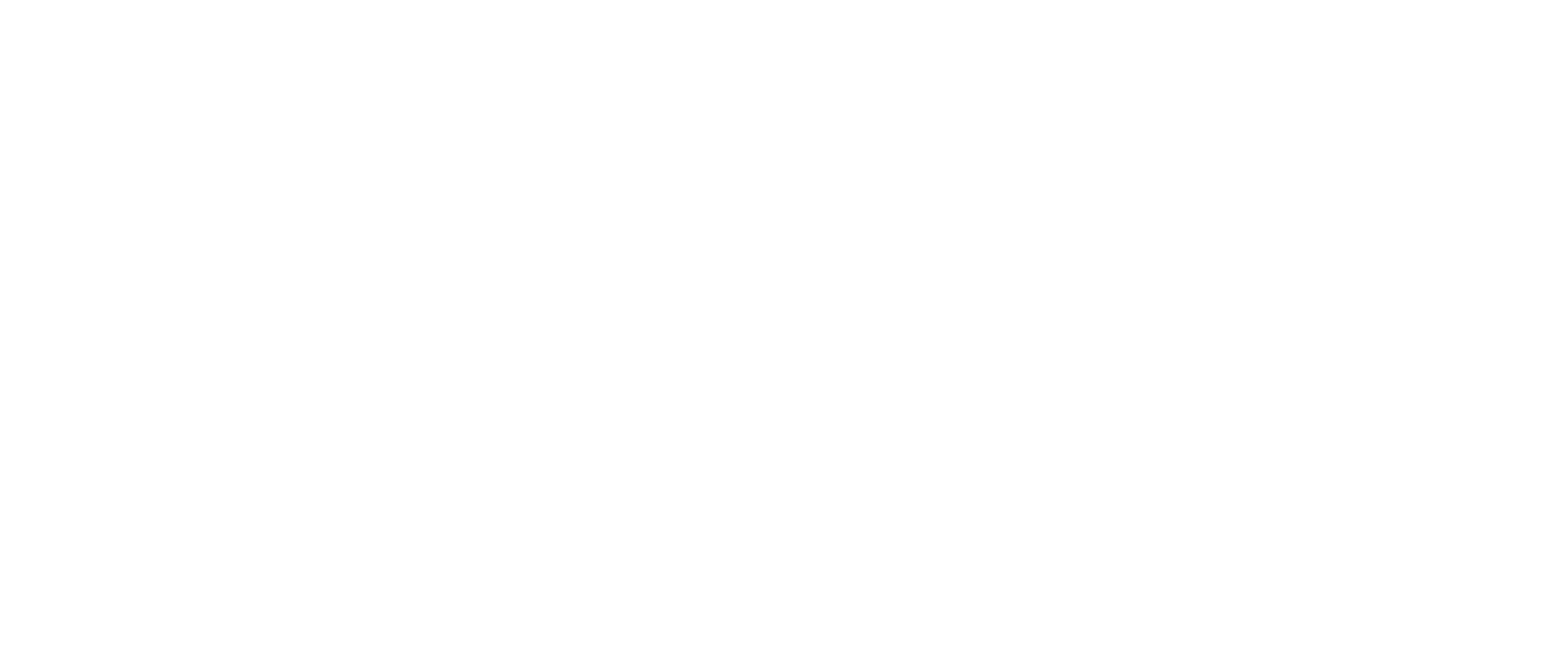
家居企业降本竞赛,谁能一“降”到底?
2023年,家居企业在承压中前行,产能过剩、原料上涨、增速放缓,不少企业直呼“压力越来越大,经营越来越难”,更有企业巨头们提出“降本增效”,让市场感受到了阵阵寒意。
在过去,“降本增效”一直是传统制造企业的必修课,尤其是那些产品同质化、身处竞争“红海”、对成本和效率极其敏感的企业,将“降本增效”上升为公司战略的一部分。现如今,这些过去习惯了高投入、快扩张,更在意技术研发、产品创新与客户体验的巨头们,也要开始“降本增效”,难题如何破解?
产能过剩已成既定事实,行业面临的困难是一样的,因此不少家居企业向生产和管理要效益,尤其是在占成本比重最大的环节“练内功”,通过降低原材料成本等多种方法,在降本增效方面不断深挖。以下分享几个实例,希望能对企业有新的启发。
01
聚焦最大成本来源:原材料一次优化率
众所周知,家具行业原材料成本依赖度较高,原材料成本约占出厂价的三分之一。其中,在原材料成本中,综合材料利用率的80%以上的取决于一次优化率。简而言之,对一次优化率进行科学化提升至关重要。
图1:基于脉云的批次大小数据分析
图2:基于脉云的批次内材料ID数分析
不难发现,目前多数管理者都把提高材料利用率局限于设备更新上,而别无他顾,导致降本增效的效果往往南辕北辙。某客户工厂经过脉云的数据采集及深度分析发现,随着批次变大,材料利用率并没有明显增加的趋势,而究其原因是由于批次内材料种类数的增加,而导致材料利用率呈下降趋势。鉴于脉云系统的分析,根据客户目前的优化和组批方式,我们建议客户优化排产和组批方法,以控制同一个批次的材料种类来改善这一情况。
材料利用率出现问题的同样还有另一家大型家居企业。数据显示,在这家企业生产车间中,小于800工件数的批次利用率普遍较低,经过脉云系统对其锯切文件深度分析后发现,由于客户采用的优化软件只设置适合大批次的优化参数,而这并不能保证所有批次类的材料利用率最大化。
因此,我们建议客户针对小于800的批次设定更适合中小批次的优化参数,配合豪迈的CutRite自动优化软件,按不同的生产需求同时配置适合的参数,提高生产效率及材料利用率,以解决材料优化率的核心问题。
发展阶段不同,任何一家企业的战略规划,都需要因地制宜,降本增效更需要有“底层思维”,这对管理者而言并不容易,要判断这一措施是否科学有效,其依据何在?这就要看它是否直接指向事物本质。
事实上,豪迈中国的脉云系统可以帮助管理者掌握这种“底层思维”,其通过获得的多维度生产数据,经过科学精准分析,助力企业更快找到产线瓶颈,也更容易找到最直接的方法,从而实现降本增效的终极目的。
02
从余料利用率入手,多角度控成本
板材成本中,综合材料利用率的10%左右取决于余料利用率,然而大部分企业采用人工实施余料管控,通常先由加料工对余料初步分拣,再由配料工进行板件数量和状况核查。由于余料规格多样,人工效率低,该分层监管方法对实际原料利用率无显著提升作用。
配合数字化余料管理软件,余料利用率提高到75%
家居产业向“余料管理”要竞争力,科凡定制给出了全套答案——其通过引入豪迈中国的余料管理系统,大板优化率从81.8%提升到86.93%,整体优化率提升至88.6%,使用余料管理前,科凡的余料利用率约为50%,而目前余料利用率为75%,节约人民币约68万,投入人工以及软件费用大概约25万/年,综合节省材料成本约43万/年。
03
降低返工率,全方位创效益
生产异常多,返工率高是定制家居存在的普遍问题。定制企业和标准化生产企业有着本质区别,定制生产本身是满足消费者需求的生产方式,但是消费者需求千差万别,导致生产的安排具有不确定性,那么出现差错往往就不可避免。
值得注意的是,超过80%的返工板件源于封边异常。据统计,在智能车间的生产线中,有超过60%的停机时间是由封边工序引起的,超过80%的返工板件是封边异常导致的,同时超过25%的投诉与封边相关,因此封边是定制家具生产过程中最为复杂的工序。
用实际加工米数精准判断封边机各个单元准确的消耗状态
做到预维保,保证封边质量
如何用好数字化工具为企业生产提高产品质量,实现降本增效,始终是豪迈中国数字化战略落地的重要使命。脉云系统经过多年的迭代,目前可通过对封边设备实时监控,收集影响封边质量的关键指数,如胶锅温度、涂胶轴温度、空压曲线、线速、预铣刀状态等数据,减少生产中不必要的停机与返工,实现降本增效。
/
豪迈中国一直是推动家居企业实现降本提效的先行者,针对能看得见的显性成本,豪迈中国通过帮助企业改善生产线、以自动化生产降低人工成本,取得了许多成功的案例。而针对看不见的隐性成本,豪迈中国利用数字化系统帮助企业发现生产过程中的瓶颈,并实现这些改进潜力,以达到降本增效。
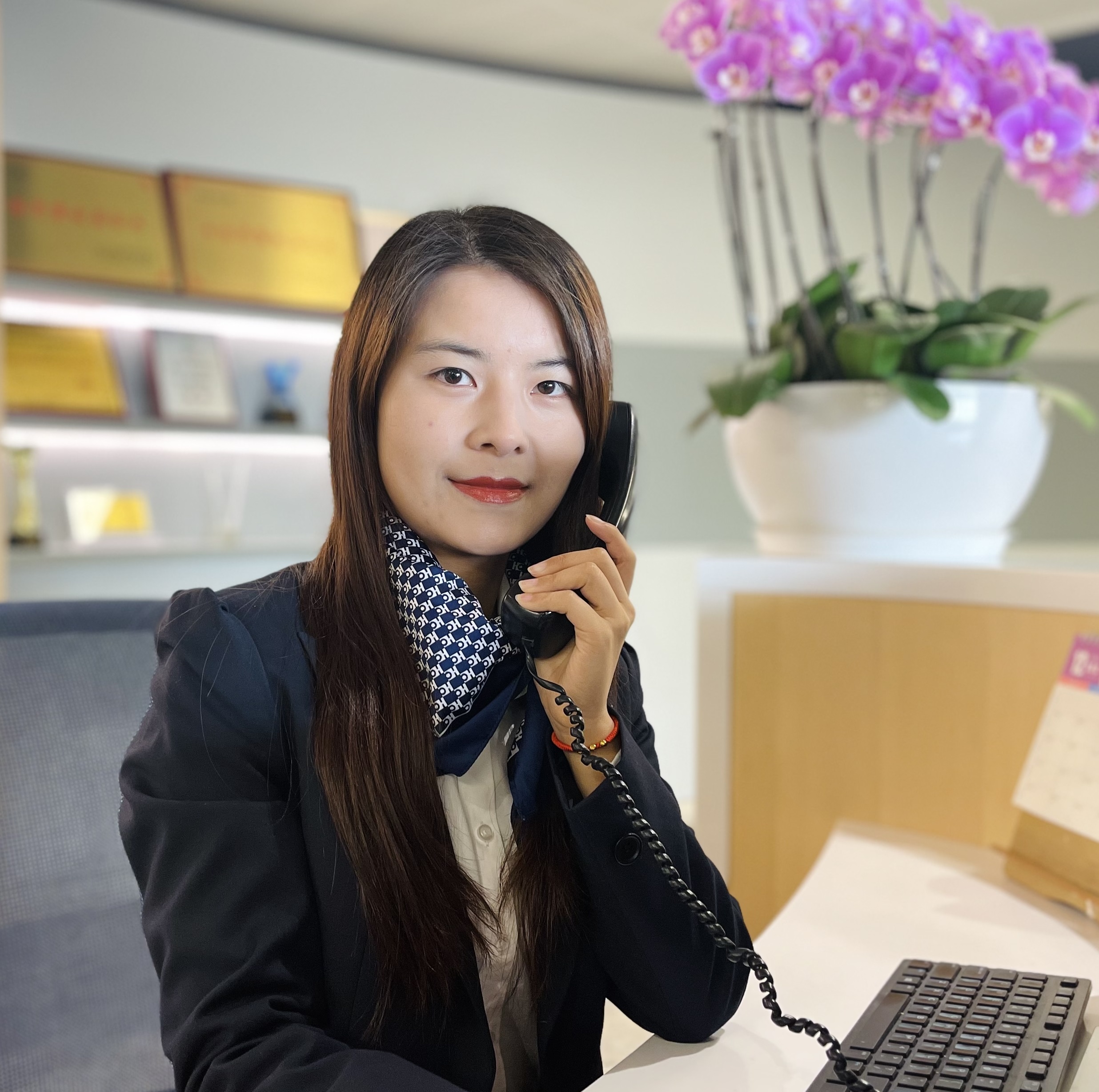